6 Types of Turbochargers
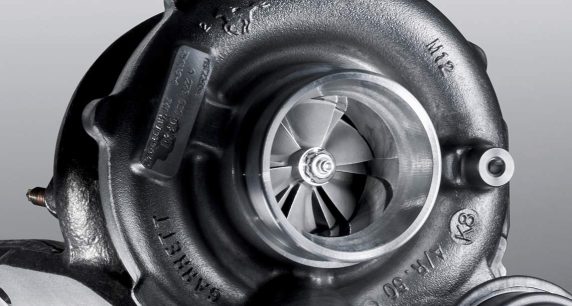
What is a Turbocharger?
Turbochargers are driven not by mechanical drive systems like the supercharger, but by the engine’s exhaust flow.
A turbocharger consists of a turbine on a shaft directly connected to a centrifugal impeller. Exhaust gas piped to the turbine inlet causes it to rotate and drive the centrifugal impeller. This impeller is similar in function to those used in centrifugal superchargers.
When engine power is demanded, engine speed increases and the increased exhaust gas flow speeds up the turbine increasing the impeller speed. This provides increased air flow to the engine enabling it to produce more power.
While a typical supercharger always runs at a speed directly related to engine RPMs (revolutions per minute), the turbocharger tends to operate at a speed related to the engine power output as demanded by the driver’s right foot.
More power desired = more exhaust flow to the turbo = increased impeller speed = more engine power.
When your car is moving on level ground at a constant speed, little boost is required. The turbocharger will become relatively passive, sort of loafing along, consuming very little energy. This enhances fuel economy.
But when you need power it comes on abundantly for accelerating up a highway ramp, for example. On a freeway trip with relatively constant cruising speeds your car will operate more economically compared to a car with a conventional supercharger.
6 Types of Turbochargers
1 . Single Turbo
The single-turbo design is discussed above. This discussion need not be repeated except to note that among the different types, this design is the most cost effective and its size makes it easiest to configure in the limited space beneath the hood of most cars.
Many turbocharged cars today use a single turbo. And we’ve seen how one manufacturer has attacked and resolved the lag problem. Single turbo cars are available from Mazda, Toyota, BMW, Volkswagen among others.
2. Twin Turbo
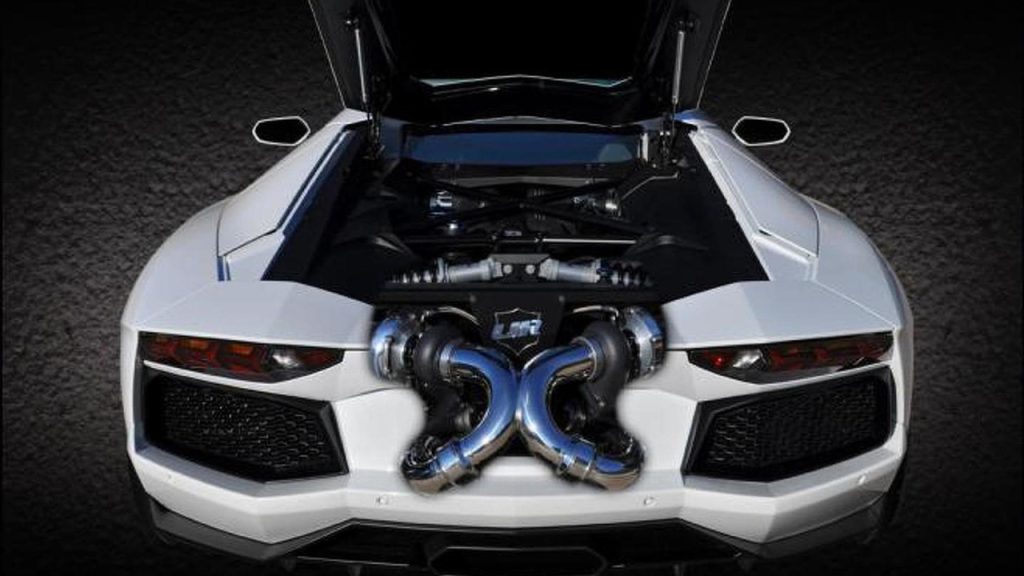
Following the oft-abused rule, “if some is good, more is better”, twin turbos simply add a second turbo to the mix.
On V-design engines (like the V-6 and V-8), one turbo is employed for each cylinder bank. Because each turbo handles half the engine’s cylinders each can be smaller than a single turbo might be for that engine. Smaller turbos have less rotating mass and will accelerate more quickly helping to minimize turbo lag.
The design and installation of two turbos is, however, more complex than a single turbo setup. More complex piping, an additional intercooler and more complex system controls increase both weight and cost of this system versus the single turbo. Underhood, space constraints are also challenged with twin turbos.
3. Twin Scroll Turbo

The exhaust flow then directed to each impeller section enters at a higher speed enabling faster turbo acceleration when power is demanded. System complexity is again required to isolate and convey independent dual cylinder exhaust flows to the impeller housing.
The impeller scroll and housing design are both more complex as well. The added complexity here increases the system’s overall cost and weight. System space needs are greater as well. This type of turbo is generally limited to inline four cylinder or V-6 engines.
4. Variable Geometry Turbo (VGT)
The variable geometry turbo incorporates a set of adjustable geometry vanes at the turbine inlet. These vanes, controlled by the engine’s PCM (powertrain control module), adjust the turbo inlet area, shrinking that area during low engine speed.
At high engine speeds the vanes open to increase the exhaust inlet area. This enables the optimum exhaust velocity to the impeller for both low and high engine speeds thus minimizing turbo lag.
Increased complexity and cost for this system are two primary drawbacks, but there is only a small size and weight penalty with the VGT design.
5. Variable Twin Scroll Turbo
This configuration has the benefit of the twin scroll inlet but includes a different approach to variable geometry.
The variable geometry feature is located in the exhaust gas piping. The exhaust flow to each scroll is controlled by an adjustable vane. At low engine speeds, this vane directs all flow to just one of the two scroll inlet ports. This enables low flow to enter the impeller at a higher speed increasing the impeller’s speed.
As engine RPMs increase and exhaust flow increases, the variable vane opens to admit more flow to the second scroll inlet. At high engine speeds full flow is directed to both twin scroll inlets.
Complexity, cost and weight are increased for this type of system. For this reason this level of complexity is only used in vehicles that demand a higher purchase price.
6. Electrically-Assisted Turbo
Electrically powered superchargers were discussed in the article referenced above. In the same way, an electric motor can also be applied to any of the above turbo configurations.
Controlled by the PCM, this motor operates to increase the turbo speed as necessary, adding boost when engine speed and exhaust flow are low. This effectively eliminates turbo lag.
The electric motor used for this application must be a design that can withstand the very high temperatures associated with a turbocharger. And here again, increased cost, weight and complexity are the drawbacks of this system.